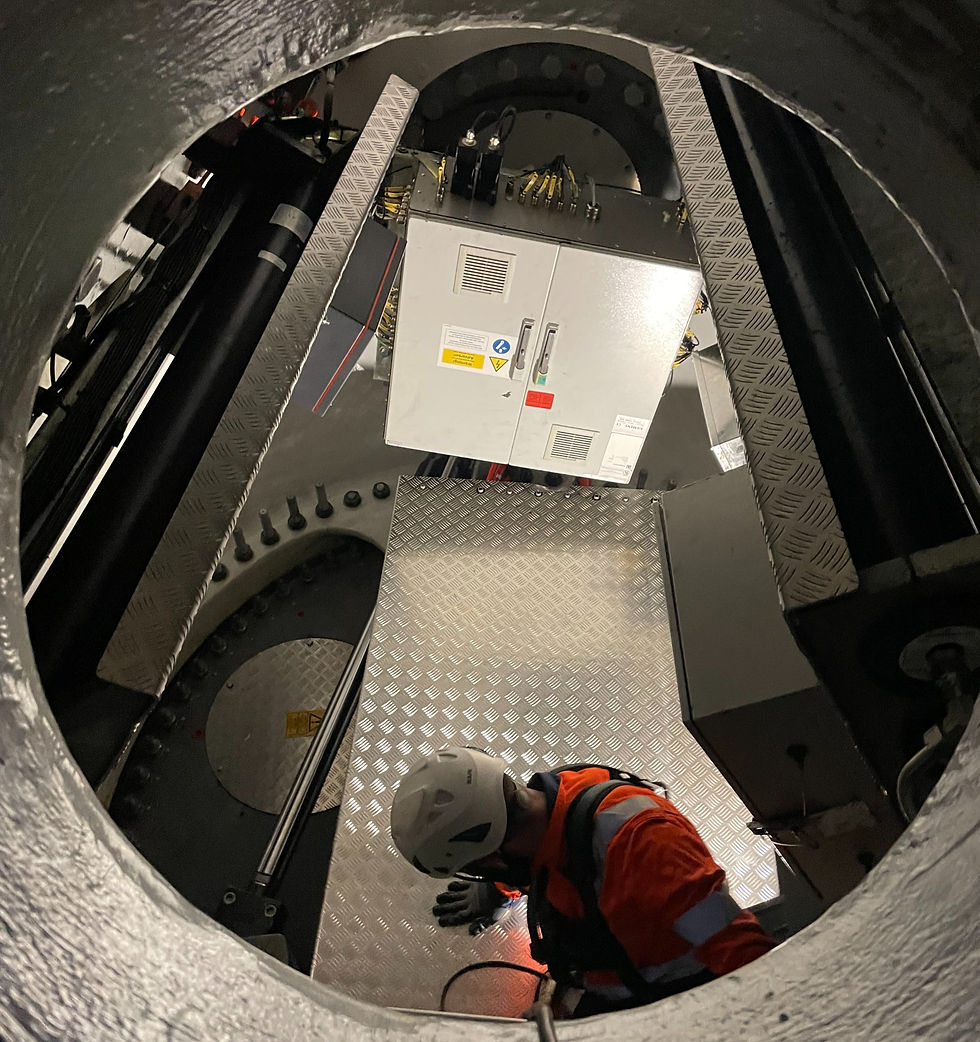
Blade Stud Failures - Assessment and Investigation
Wind turbine blade connections are notoriously challenging to manage with regular integrity problems and difficult maintenance access.
Blade to blade bearing connections suffer more fastener failures than any other structural joint on wind turbines.
Failed fasteners can result in significant consequential damage to safety critical pitch systems, necessitate unplanned turbine downtime and can often be problematic to remove.
Fatigue is the primary cause of failure and is highly dependent on maintaining the correct preload within the fastener during installation and throughout operational life. Blade fasteners are often challenging to install and maintain, requiring access to the rotor hub which requires complex manipulation of tools and equipment with challenging access routes into a highly restrictive working space.
Current practices for the correct management of preload are imprecise, requiring time consuming periodic retightening without good control of the resultant preload increasing the risk of fatigue failures.
Responding to the challenge EchoBolt has been able to develop a method to provide a comprehensive assessment of blade connection integrity, not only identifying opportunities to improve the management of preload but also identifying fasteners with existing defects to allow resolution before failure.
An entirely new strategy of blade bolt integrity management based on periodic ultrasonic inspection offers the potential to eliminate over 80% of maintenance costs, reduce safety risks to operations personnel whilst simultaneously improving asset integrity though eradicating fastener failures.
At EchoBolt we are constantly looking for ways to help our customers with their biggest integrity challenges. Through the development of a comprehensive wind turbine blade connection integrity assessment we have been able to help customers eliminate failures and significantly reduce maintenance interventions.
Pete Andrews - Managing Director
Project Gallery







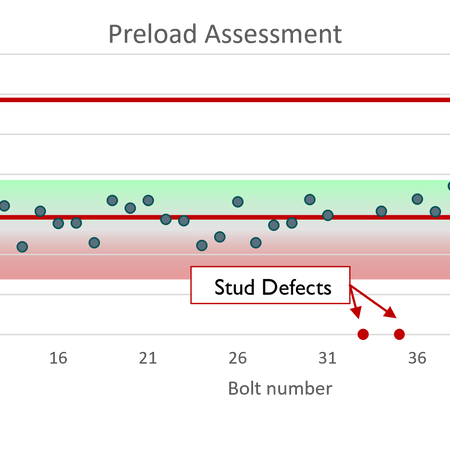

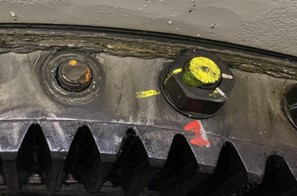
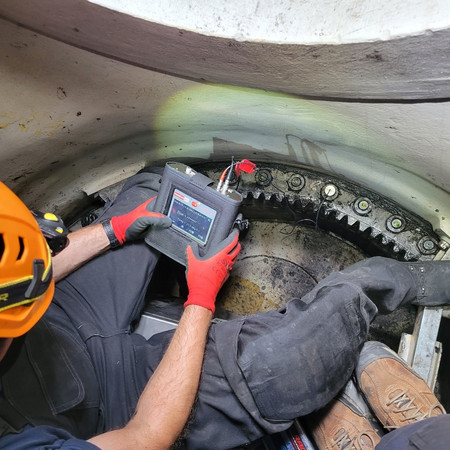
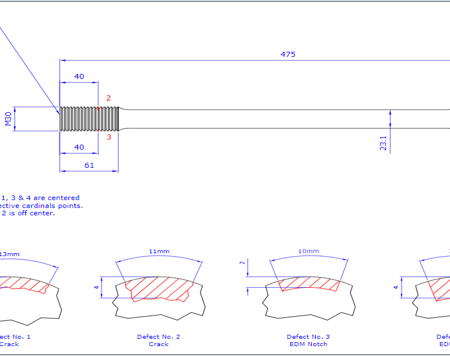